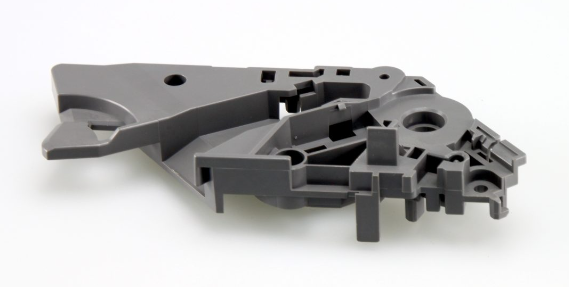
In this section we answer these questions and show you common examples of injection molded parts so you can familiarize yourself with the basic mechanics & applications of the technology.
What is injection molding?
Injection molding is a formative production technology: to create a part, plastic is first melted and then injected into the cavity of a mold. As the material cools, it solidifies and assumes the geometry (shape) of the mold. The part is then ejected and the process starts again.
This is a fundamentally different production method from the additive (3D printing) or subtractive (CNC milling) technologies. The flow and solidification of the material during injection has a significant impact on the major design constraints for this technology.
The injection molding process
Injection molding services are widely used today for both consumer products and technical applications. Almost every plastic item around you is produced by injection molding. This is because the technology is able to produce identical parts in very large numbers (typically, 1,000 to over 100,000 pieces) at a very low cost per part (typically around $ 1-5 each).
However, compared to other technologies, injection molding start-up costs are relatively high, especially as custom tooling is required. The cost of a mold can range from $ 3,000 to over $ 100,000, depending on the complexity, material (aluminum or steel) and accuracy (prototype, pilot run, or large-scale production mold).
All thermoplastics can be injection molded. Certain types of thermosets and liquid silicones are also suitable for the injection molding process. The most commonly used materials in injection molding are:
Polypropylene (PP): ~ 38% of global production
ABS: ~ 27% of global production
Polyethylene (PE): ~ 15% of global production
Polystyrene (PS): ~ 8% of global production
Even considering all other possible manufacturing technologies, injection molding using only these four materials accounts for over 40% of all plastic parts produced annually worldwide!
Advantages of injection molding - Mass production of plastics
Injection molding is the most cost-effective technology for producing high numbers of identical plastic parts. Once the mold has been made and the machine set up, additional parts can be produced very quickly and very economically.
The recommended minimum production volume for injection molding is 500 pcs. This is where economies of scale emerge and where the relatively high initial cost of tooling has a less pronounced effect on unit price.
© 2025 HNGN, All rights reserved. Do not reproduce without permission.